Cosa è un Digital Twin e perché è importante nell'industria
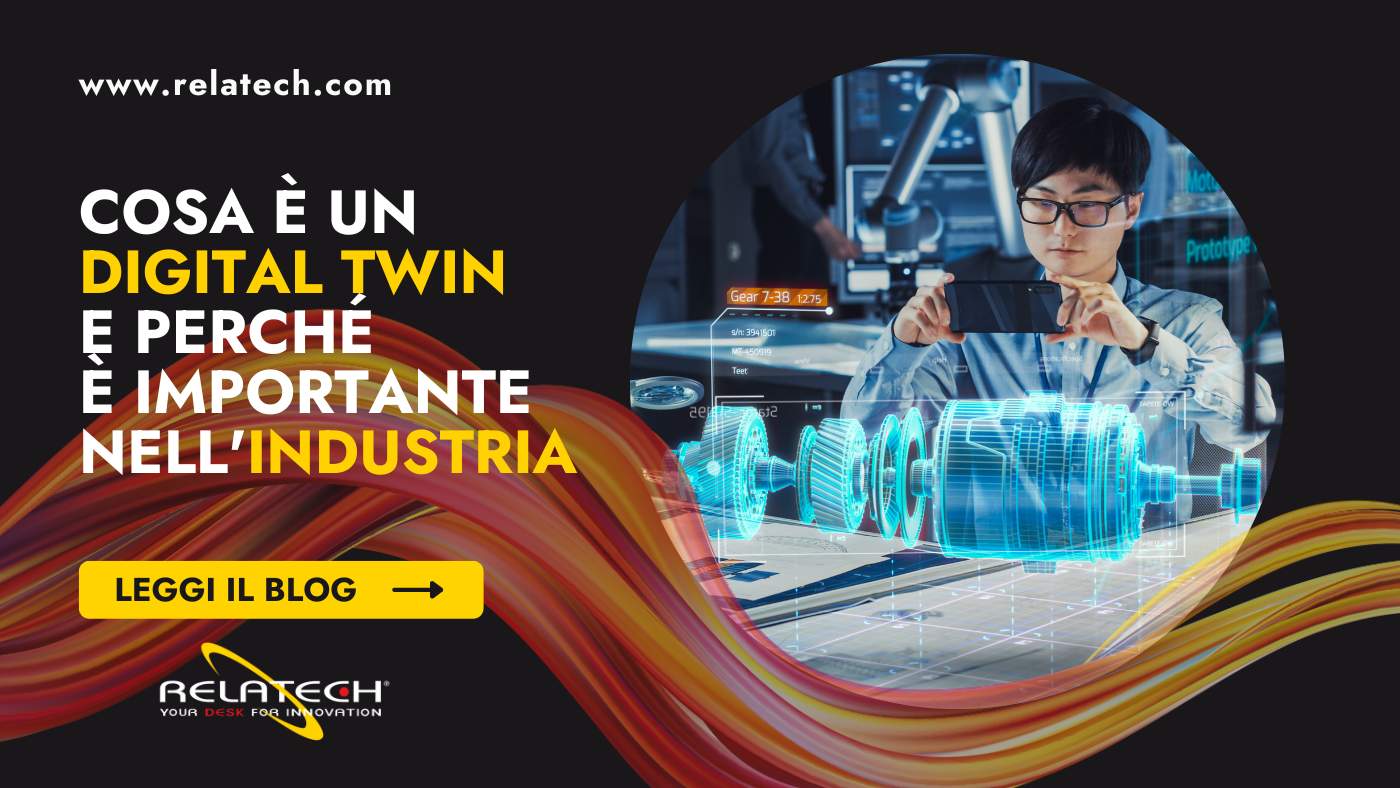
A cura della direzione marketing Relatech
Il rapido progresso tecnologico, in particolare nel settore dei Big Data, negli ultimi anni ha portato alla popolarità del concetto di Digital Twin. Questo "gemello digitale" è una replica virtuale di un sistema, con tutte le informazioni e le caratteristiche necessarie.
Il mercato globale del Digital Twin valeva 9,7 miliardi di dollari nel 2022, ma raggiungerà 185,78 miliardi di dollari entro il 2031, crescendo ad un CAGR del 38,8% tra il 2023 e il 2031, secondo lo studio di Straits Research. Un altro studio di Global Insight Market conferma questo trend di crescita esponenziale, solo con numeri leggermente rivisti ma comunque alti.
La diffusione principale dei progetti di Industria 4.0 si è avuta soprattutto nel settore Operativo (OT) permettendo la connessione degli impianti industriali e la rilevazione continua dei loro dati di funzionamento.
Un numero ancora limitato di imprese, tuttavia, si è invece spinto oltre utilizzando tali dati all’interno di sistemi di gestione e controllo della produzione per una digitalizzazione completa dei processi produttivi.
Ma cos’è esattamente un Digital Twin e perché le imprese del mondo industriale, comprese le PMI, dovrebbero valutarne attentamente l’utilizzo?
Cosa è un Digital Twin?
Un Digital Twin è la rappresentazione digitale di un oggetto fisico. In ambito industriale può trattarsi di un dispositivo, di una macchina, o un insieme complesso di elementi che costituiscono ad esempio una linea di produzione fino ad un intero impianto.
Un digital twin può essere generato a partire da dati relativi alle caratteristiche fisiche e meccaniche, ottenuti in generale tramite disegni CAD-3D, e al funzionamento atteso tramite modelli termodinamici, elettrici o altro, ottenibili tramite altri strumenti di progettazione.
Spesso, tuttavia, questi modelli per quanto precisi non riescono a rappresentare in modo del tutto corretto il comportamento in produzione, soprattutto nel caso di sistemi molto complessi. Per tale motivo recentemente l’industria si è concentrata maggiormente sullo sviluppo di Digital Twin ottenuti a partire da dati di funzionamento reali.
Si parla in questo caso di modelli Data Driven. I dati vengono acquisiti tramite dispositivi di monitoraggio e sensori installati sull'oggetto fisico che raccolgono e trasmettono i dati in tempo reale a sistemi di elaborazione e analisi dati, solitamente disponibili in cloud, che generano il modello data driven.
L’adozione dell’approccio data driven è stato accelerato notevolmente negli ultimi anni dallo sviluppo di diverse tecnologie.
Innanzi tutto, dall’utilizzo sempre più diffuso di dispositivi di Industrial IoT, quali sonde e sensori di rilevazione dati sempre più precisi, sistemi di connettività e gateway industriali in grado di connettere macchinari di ogni tipologia e tecnologia, raccogliere e pre-elaborare i flussi di dati, convertirli fra diversi protocolli industriali ed infine inviarli ai sistemi di elaborazione centralizzati.
In tal modo, oltre a monitorare e analizzare il comportamento e le prestazioni dell'impianto fisico, è possibile raccogliere grandi volumi di dati storici di funzionamento e sottoporli a metodi di analisi evolute al fine di correlate tipologie di dati apparentemente indipendenti, analizzare trend ed infine ottenere appunto un modello di funzionamento del sistema basato sui dati effettivi.
Quest’ultimo risultato, a sua volta, è reso possibile da un lato dalla costante evoluzione degli algoritmi di intelligenza artificiale, in particolare di machine learning e delle reti neurali; dall’altra dalla disponibilità di sistemi di Big Data Analytics e di infrastrutture in cloud sempre più performanti. Grazie a queste tecnologie avanzate, è possibile generare dei Digital Twin basati sui dati e utilizzarli per trovare anomalie, prevedere guasti, ottimizzare le operazioni e migliorare l'efficienza complessiva.
Un punto debole dei modelli Data Driven, tuttavia, è che, pur dando risultati potenzialmente molto accurati, spesso questi sono di difficile interpretazione in termini operativi.
Per questo motivo è necessario adottare anche delle tecniche, dette di Explanation, per ricondurre i risultati del modello data driven ai parametri più tipici del modello fisico, e più vicini alla cultura del mondo industriale. E’ necessario quindi creare una ricorsione continua fra mondo fisico e virtuale per ottenere da un lato un Digital Twin sempre più accurato nell’interpretazione dei dati, dall’altro un modello operativo efficace e realmente utilizzabile da parte degli operatori di campo.
Vantaggi offerti dai Digital Twin nell’industria
I Digital Twin possono essere utilizzati nella maggior parte dei settori industriali, come il manifatturiero, l’automotive, la logistica, l'energia, l'aviazione e molto altro. Macchine complesse, linee di produzione, impianti energetici e reti di distribuzione possono essere modellate e analizzate attraverso questi nuovi sistemi.
Alcuni dei vantaggi principali ottenibili dallo sviluppo e adozione dei Digital Twin sono:
- Simulazione: un Digital Twin, permette di effettuare simulazioni del funzionamento dell’impianto approfondendo alcune tipologie di comportamento difficilmente osservabili direttamente sul sistema fisico in produzione.
- Ottimizzazione: la raccolta di dati reali durante il funzionamento del sistema e la loro analisi tramite i modelli Data Driven consente di identificare aree di miglioramento e di ottimizzare le operazioni per massimizzare l'efficienza abbinate a metodi di produzione lean.
- Previsione: l’utilizzo di algoritmi previsionali permette ad un Digital Twin di prevede trend in anticipo, rispetto ai sistemi tradizionali. Ad esempio è possibile prevedere guasti o esaurimento di scorte, permettendo di effettuare interventi preventivi e ridurre i tempi di fermo delle macchine.
- Riduzione dei Costi: la prevenzione dei guasti e l'ottimizzazione delle operazioni riduce gli interventi di manutenzione e i tempi di fermo macchina connessi, permettendo così un’importante riduzione dei costi operativi.
Secondo uno studio di Capgemini, condotto tramite survey su un campione di 800 aziende che utilizzano questa tecnologia, le organizzazioni che utilizzano il Digital Twin hanno registrato in media un miglioramento del 25% nelle prestazioni del sistema e un miglioramento del 15% nei risultati operativi e di vendita.
Inoltre, i Digital Twin offrono un'opportunità unica per combinare sostenibilità e crescita redditizia. Utilizzando queste soluzioni, le organizzazioni hanno ottenuto in media un miglioramento sull’utilizzo dei consumi delle risorse e quindi delle metriche di sostenibilità del 16%.
I risultati del report di Capgemini mostrano inoltre come l’utilizzo delle analitiche dati nel Digital Twin sia un vantaggio competitivo enorme, consentendo di prendere decisioni basate sui dati lungo tutto il ciclo di vita e attraverso gli ecosistemi della produzione.
Queste le funzioni chiave migliorate dall’uso dei Digital Twin secondo le aziende intervistate.
Casi d’uso dei Digital Twin nell’Industria
Il Digital Twin di un macchinario o impianto industriale può risultare estremamente utile in tutte le fasi del suo ciclo di vita fisico:
- In fase di progettazione la copia digitale del macchinario può essere utilizzata per prototipare idee, condurre simulazioni e test virtuali, migliorando l'affidabilità del prodotto finale.
- In fase di pianificazione dell’installazione può aiutare a valutare l'ergonomia, misurare gli ingombri dell’assemblato e l'interazione del sistema con l’ambiente, evitando sorprese all’atto dell’installazione fisica.
- In fase di avviamento il Digital Twin permette di supportare le attività di configurazione remota dell'apparecchiatura e il training agli operatori in campo.
- Durante l’esercizio permette di effettuare un monitoraggio predittivo e di anticipare possibili malfunzionamenti. Inoltre, incrociando i dati di esercizio con quelli economico-finanziari provenienti dai sistemi gestionali, può fornire analitiche sui KPI di business supportando il management nei processi decisionali.
- Durante la manutenzione può assumere inoltre un ruolo fondamentale aiutando ad ottimizzare e velocizzare le attività operative, riducendo gli errori manuali e prevenendo i guasti, grazie a diagnosi preventive a distanza e ordini automatici di pezzi di ricambio.
- Infine, il Digital Twin può aiutare anche nel processo di dismissione e fine vita del prodotto, consentendo di prendere decisioni informate sul riutilizzo, il ricondizionamento, il riciclaggio o la rottamazione dei componenti.
Relatech
Il gruppo Relatech supporta i clienti nel processo di innovazione digitale tramite un modello di Business che unisce tecnologie digitali abilitanti, soluzioni innovative e know-how costantemente aggiornato.
Grazie alla propria soluzione ReFab per la Smart Industry, Relatech è in grado di affrontare tutte le sfide concernenti la realizzazione di un Digital Twin, dall’acquisizione dei dati dagli impianti fisici, al trasferimento sicuro sui sistemi in cloud, fino all’analisi tramite algoritmi di machine learning e alla visualizzazione dei modelli 3D, utilizzando tecnologie di realtà aumentata e virtuale.
L’esperienza fatta sul campo con diversi clienti importanti ci rende il partner ideale per intraprendere il processo di trasformazione digitale indispensabile per aumentare la competitività di ogni impresa.