AR and VR for industry: how production processes improve
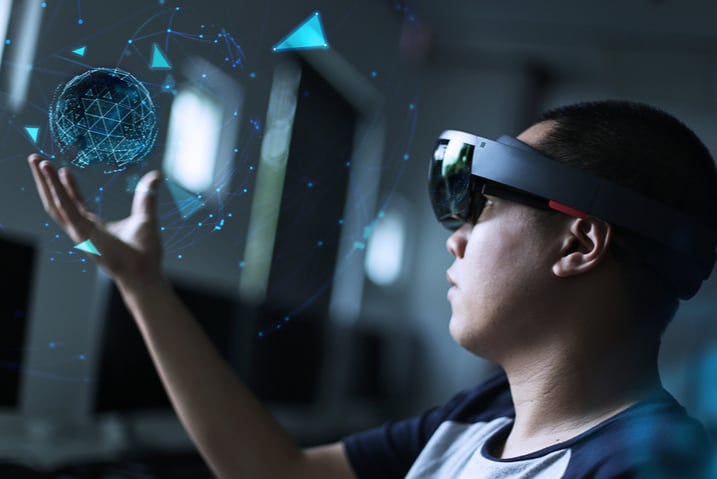
AR and VR for industry are the new frontiers for optimizing production processes in the manufacturing world and beyond. Augmented Reality and virtual reality in fact combine to define that digital twin model according to which every physical entity can be replicated digitally with a "twin" that represents it. The potential of this model lends itself to various fields of application, but in the industrial sector they have so far shown one of the most promising contexts.
Added to this is the thrust of the pandemic crisis which, due to the reduction in attendance in the workplace, including factories, has emphasized the value of remote activities and remote assistance. A modality that the use of AR and VR in industry make practicable and that, indeed, will most likely represent the usual form even in the "new normal". To understand this, one of the most obvious examples is that offered by maintenance in industrial plants.
How AR and VR support predictive maintenance
Generally any intervention on the machinery of the plants, especially the extraordinary and unscheduled one, requires the use of a manual that the operator must consult to deal with a system anomaly. The impact of this method on the times of machine downtime, and therefore on the production processes, is very onerous. It has been calculated that unexpected downtime can cost manufacturing up to $50 billion a year and that the main cause of downtime in 42% of cases is an unplanned failure.
AR and VR, on the other hand, make it possible to minimize these downtimes, equipping field workers with tools to support predictive maintenance. In particular, augmented reality makes it possible to monitor each system on a tablet or through Hololens with all the operating indicators superimposed, including those from which alarms could be generated when a value (temperature, pressure, wear, etc.) becomes out of order. norm.
AV and VR in the industry, from training to design
Augmented Reality makes it possible, for example, to anchor on the floor of your office or in a place far from where the machinery is located, a virtual reproduction of it around which you can move, simultaneously receiving all the parameters that refer to its functioning.
Virtual Reality, on the other hand, reproduces exactly the entire environment in which the device is placed and is very suitable as a training tool, since it faithfully illustrates, albeit digital, all the operations and interventions that must be implemented in the physical context in the which one you already work or will go to work. Furthermore, VR today is spreading in the design phases, as it creates virtually all the conditions of a product or process before installation or implementation takes place. In this way, possible errors or malfunctions can be anticipated that would otherwise affect the production processes once started.
The use of AV and VR in Relatech's ReFab 4.0 system
ReFab 4.0 is Relatech's solution designed for the acquisition, monitoring and analysis of large amounts of data through machine learning algorithms for the prediction of possible malfunctions within industrial processes. ReFab 4.0 also adopts AR and VR technologies in order to enable predictive maintenance and to be used for effective training of the workforce.
In particular, through the AR Digital Twin Monitoring function, REFab 4.0 helps employees to constantly monitor the devices by reporting a 3D image for each one accompanied by a series of values that record their progress in real time.
Another function, the AR SOP Assistant, assists the operator in carrying out any procedure on a machine, giving animated suggestions on the components that show a possible anomaly and on the operations to be carried out, including the equipment needed to replace them. if the system deems it necessary. Information that, if promptly communicated, avoids those periods of downtime that have negative repercussions on productivity and efficiency.
Finally, the ARsistant of ReFab 4.0 allows you to use AR or VR technologies to communicate, sharing the same system, the field worker with a more experienced technical figure who can guide him remotely in carrying out particularly complex activities.
In conclusion, the use of AR and VR technologies in the industrial world allows to obtain considerable benefits in terms of more effective training of operators on the most frequent maintenance activities to be carried out, guided support during operations and online help for carrying out the activities. more complex, reduction of manual errors during operations and of the overall downtime.